СКАЗАНО!
Президент Беларуси Александр Лукашенко:
— Похожая ситуация и в сфере производства лыж и другого спортивного инвентаря на предприятии «Телеханы». Надо обязательно совершенствовать работу и выходить на более высокий уровень. Мы все-таки относительно северная страна, надо, чтобы детишки, как и мы с тобой когда-то, занимались на улице. А улица сегодня — это лыжи прежде всего. Надо со школьных лет прививать им эти знания, опыт для того, чтобы просто здоровые люди были. А не сидели в интернете и не тыкали в телефон.
2 февраля 2024 года, во время доклада управляющего делами Президента Беларуси Юрия Назарова
Президент Беларуси Александр Лукашенко:
— Похожая ситуация и в сфере производства лыж и другого спортивного инвентаря на предприятии «Телеханы». Надо обязательно совершенствовать работу и выходить на более высокий уровень. Мы все-таки относительно северная страна, надо, чтобы детишки, как и мы с тобой когда-то, занимались на улице. А улица сегодня — это лыжи прежде всего. Надо со школьных лет прививать им эти знания, опыт для того, чтобы просто здоровые люди были. А не сидели в интернете и не тыкали в телефон.
2 февраля 2024 года, во время доклада управляющего делами Президента Беларуси Юрия Назарова
Повернули на экспорт
Ежегодно филиал выпускает до 20 тысяч пар лыж под любой вес и рост. Предприятие занимает до 80 процентов белорусского рынка: лыжи поставляются в школы, торговые точки, пункты проката, часть уезжает в Россию. Последние полгода технологи и дизайнеры разрабатывали новую, улучшенную линейку. Первые 150 пар уже сошли с конвейера. Директор ГП «Беларусьторг» Денис Гордеев рассказал о перспективах:— С учетом того что мы фактически обеспечиваем потребности рынка Беларуси, увеличение объемов производства напрямую зависит от выхода на новые рынки сбыта. Сейчас активно осваиваем маркетплейсы. На популярных российских площадках теперь можно приобрести лыжи «Телеханы». С выпуском нашего нового бренда мы делаем шаг вперед, думаю, потребители также оценят ребрендинг. Он позволит нам не только продвигать продукцию в России, но и начать вести переговоры с крупной российской сетью, которая занимается дистрибуцией спортивных товаров.
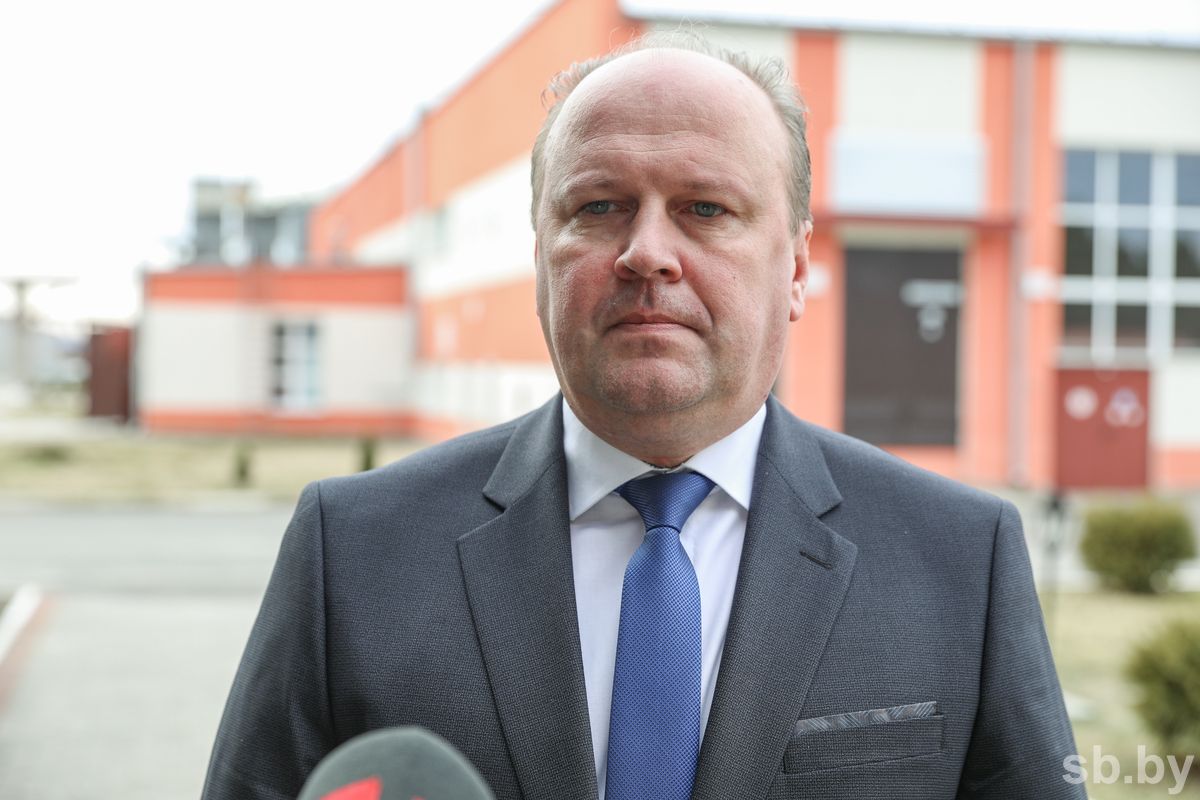
К слову, новый бренд уже успел пройти испытания всех технических и механических свойств: жесткость, кручение, излом, прочность. За качеством изделий специалисты следят строго. А оно напрямую зависит от каждого компонента, поэтому все операции в цеху производства пластиковых лыж автоматизированы. На четырех участках установлено современное оборудование от ведущих зарубежных и отечественных производителей.
Без внутреннего напряжения
Весь процесс — от древесной заготовки до выхода конечного продукта — занимает три дня. В производство лыжи запускаются партией — 3—3,5 тысячи пар в месяц. На первом участке изготавливают средний клин. Для лыж массового потребления его делают из осины — одного из наиболее легких древесных материалов. Первым делом на заготовках сотрудники устраняют все дефекты. Сучки и трещины помечают карандашом, а после дело за техникой: считывает линии и режет специальный станок. Неподходящие по размеру и качеству детали и обрезки собирают в контейнер для использования в виде топлива в собственной котельной, а заготовки длиной от 15 сантиметров отправляются на линию сращивания.Склеенные между собой заготовки намного качественнее цельного бруска. Такой способ убирает «внутреннее напряжение» в древесине, придает необходимую жесткость и предотвращает растрескивание. А после попадания на четырехсторонний продольно-фрезерный станок и высокоточный обрабатывающий центр заготовку уже совсем не узнать! Из прямоугольной она превращается в трапециевидную — тот самый средний клин. Заместитель директора Станислав Радюкевич объясняет:
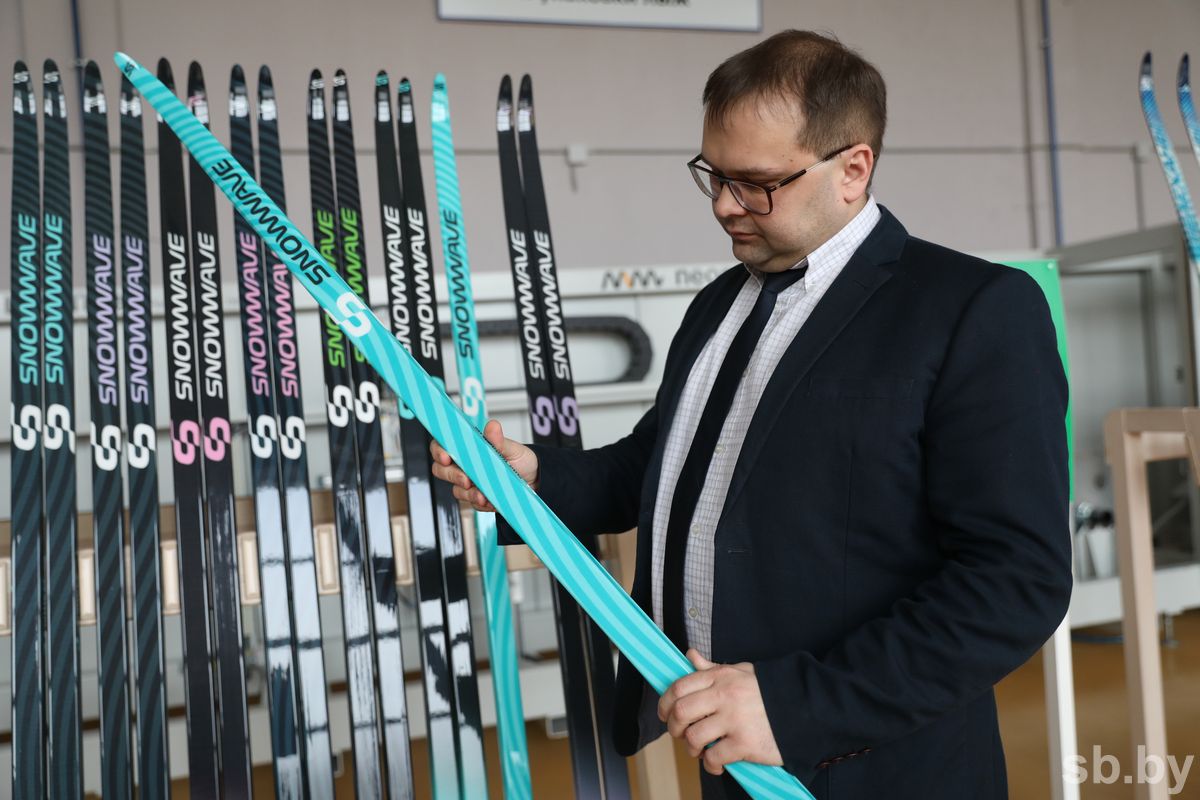
— Геометрия — первое и основное, что задает форму лыж, от этого во многом зависит скольжение и качество хода. В новой линейке мы ее усовершенствовали по многим параметрам: ширину лыжи сделали уже, увеличили угол наклона боковых поверхностей до четырех градусов. Это позволяет правильнее расположить комплектующие внутри лыжи и получить на выходе более изящный и интересный внешний вид.
Разница между новым средним клином и его предшественником отчетливо ощущается даже в руке — у обновки вес уменьшился сразу на 15 процентов. И если в прошлом сезоне лыжа весила около 800 граммов, то теперь не превышает 680—720 граммов. Добиться этого получилось и за счет увеличения пластиковых носковой и пяточной частей. На готовый средний клин пластиковые носок и пятка наплавляются в специальных формах путем расплавления гранул при температуре до 270 градусов.
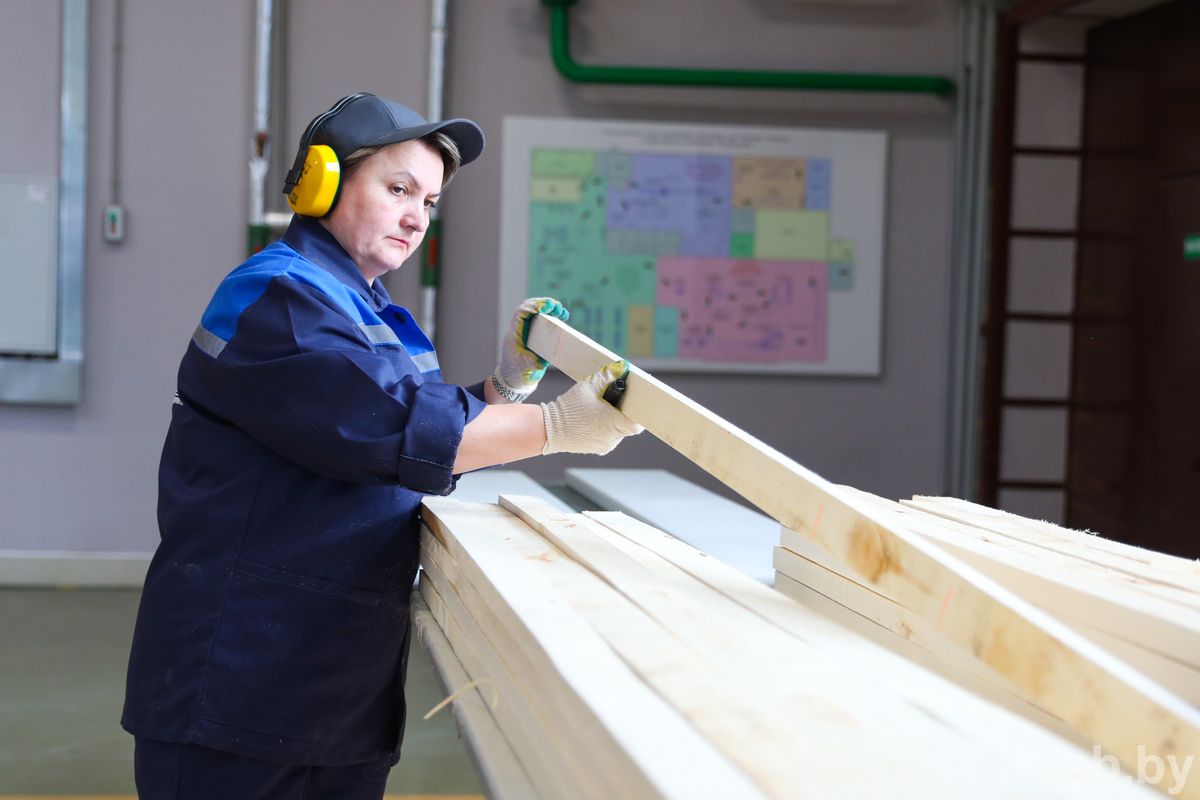
— На следующем участке придаем будущим лыжам жесткость, — продолжает экскурсию Станислав Радюкевич. — Пластиково-деревянную заготовку (средний клин) специалисты заворачивают в препрег — это склеивающий и армирующий материал, пропитанный эпоксидными смолами. В прессовочных машинах, которые специально для нас разработали в ОАО «Кузлитмаш» (предприятие холдинга «БЕЛАЗ-Холдинг»), спортинвентарь выдерживается 20 минут при температуре 115—125 градусов. После чего каждый экземпляр обрабатываем по периметру алмазным инструментом, шлифуем нижнюю скользящую поверхность и наносим структуру.
Виды «снежной волны»
Наши лыжи на финишной прямой, а точнее, на участке отделки и подготовки компонентов. Для повышения износостойкости здесь их покрывают лаком и сушат под УФ-лучами. Теперь новенькие комплекты можно отправлять на упаковку. Там уже красуются выпущенные 150 пар. В ближайшее время все четыре типоразмера уедут на обкатку к спортсменам:— Эта линейка предназначена для масс маркета, поэтому пока изготавливаем самые ходовые экземпляры: 1600, 1700, 1800 и 1900 сантиметров. А как изучим спрос, при необходимости увеличим размерный ряд. Министерство спорта первым опробует наш новый продукт в деле, после этого будем наращивать объемы производства.
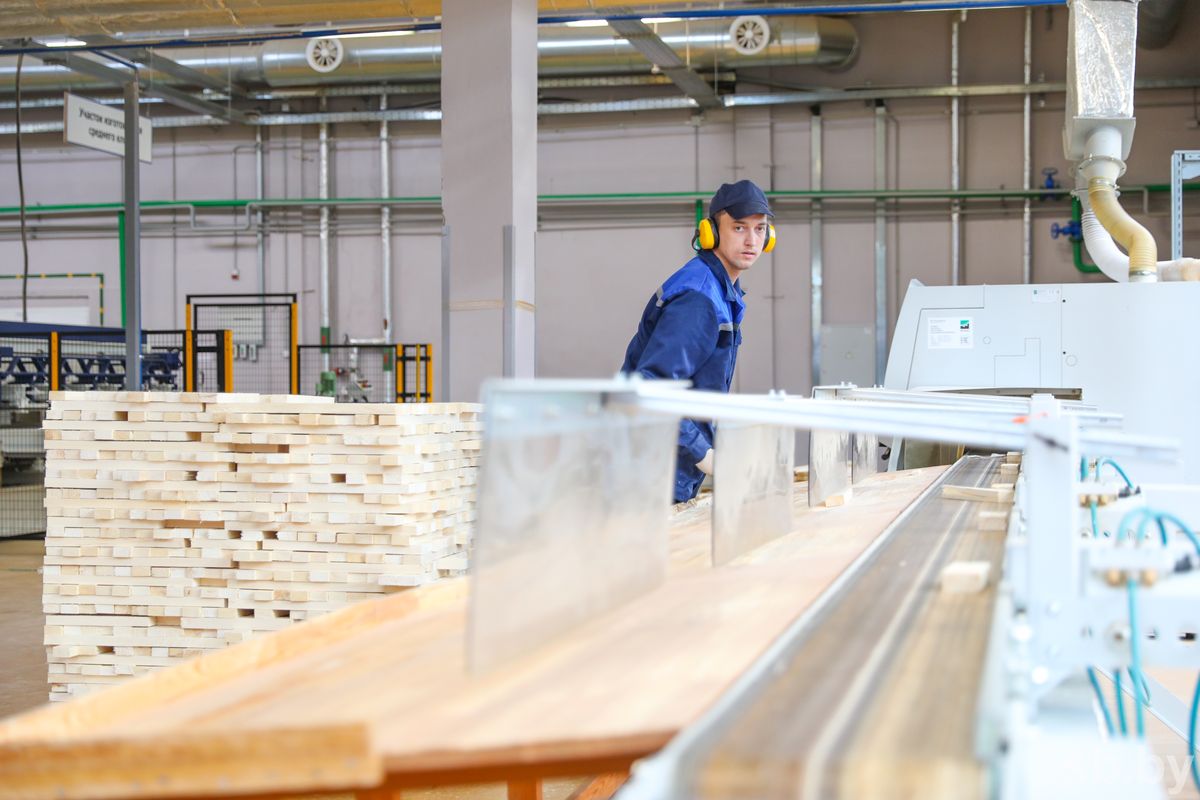
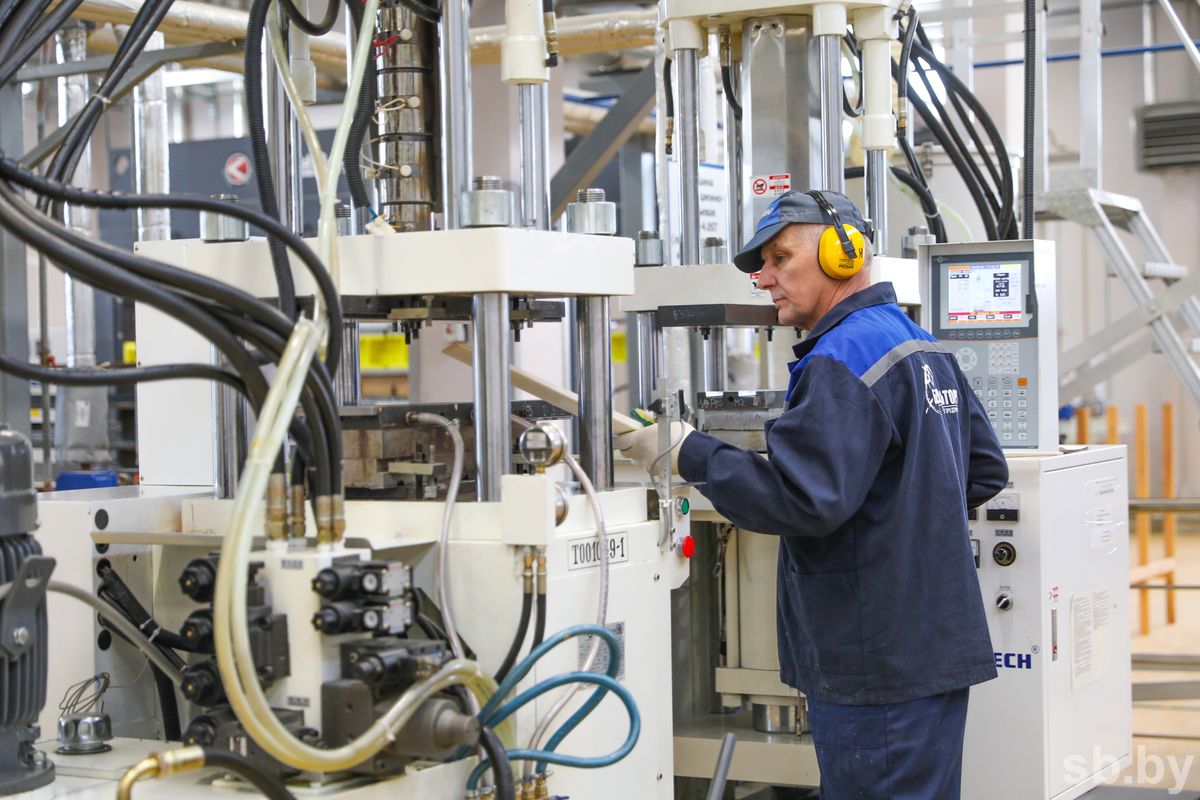
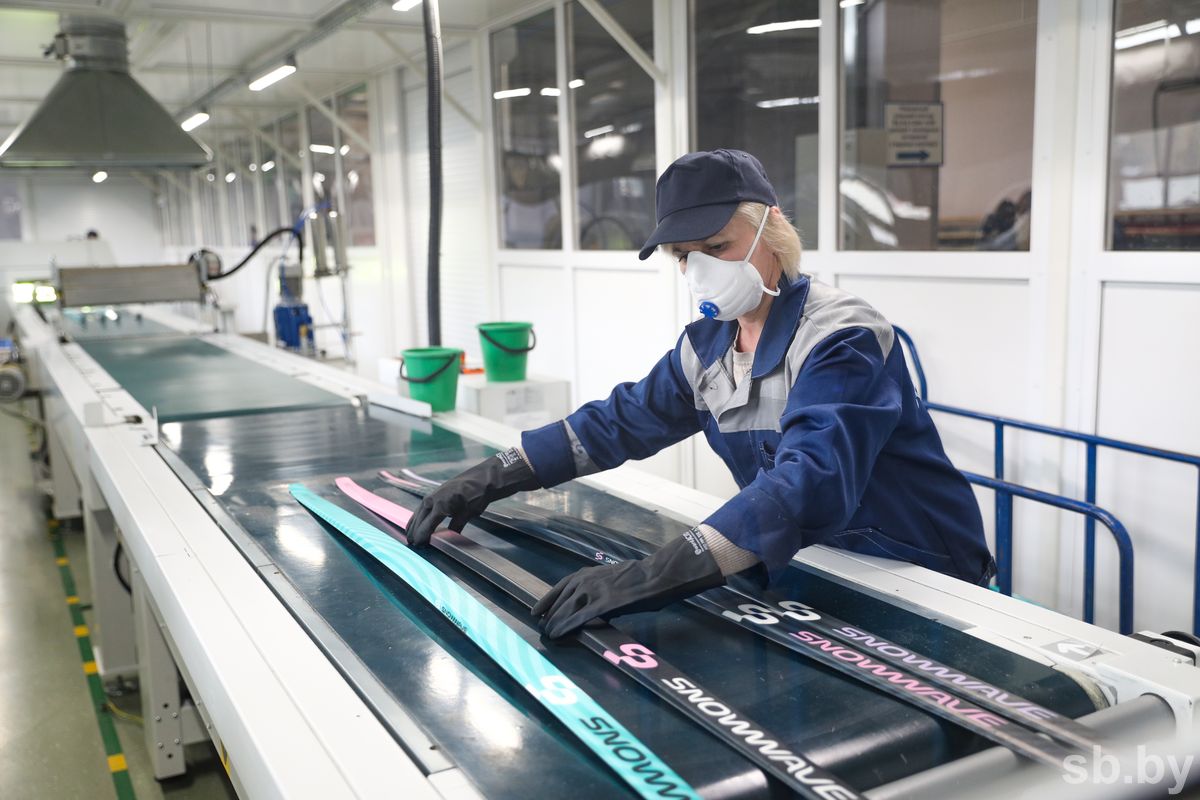
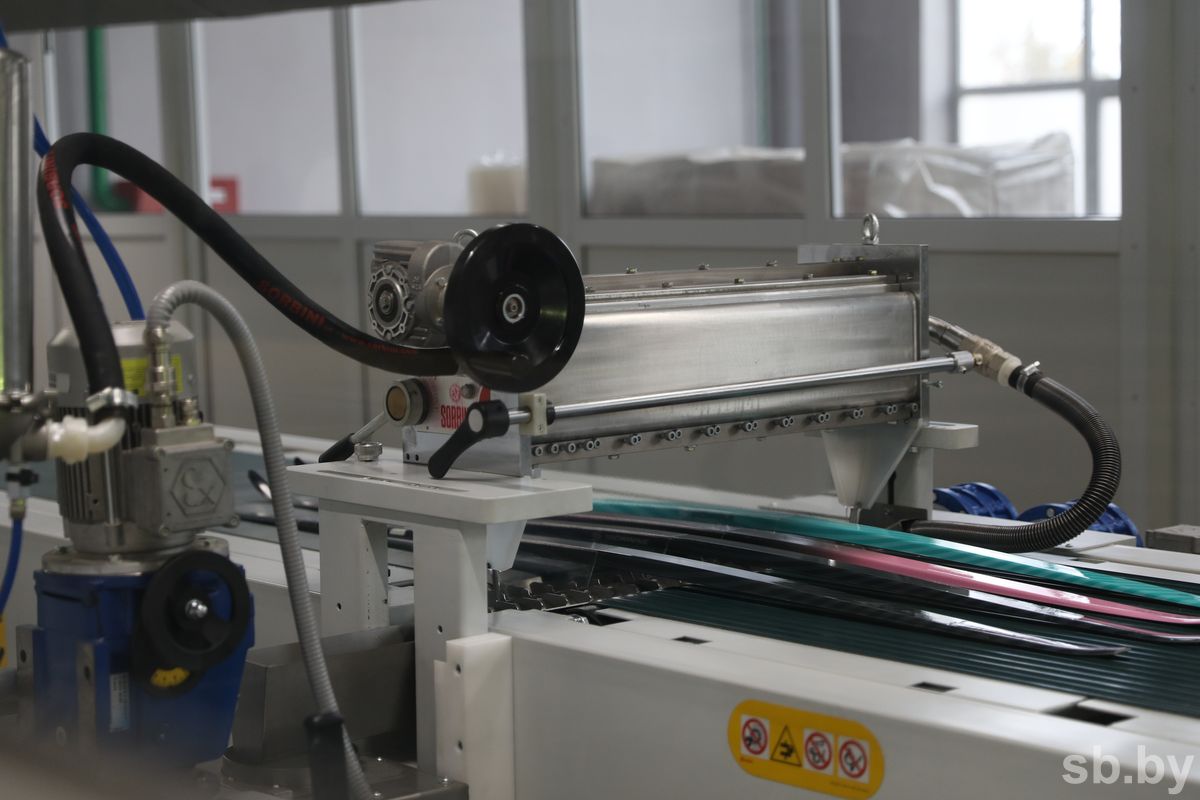
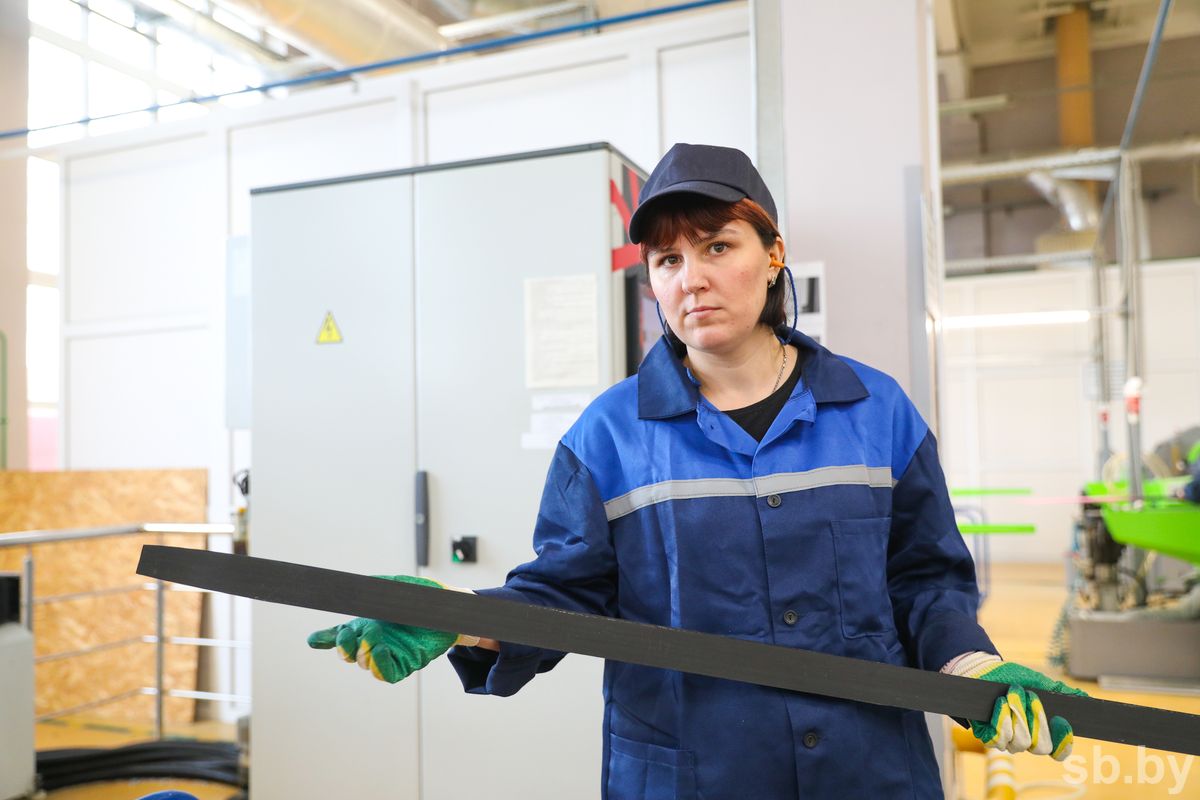
lukashik@sb.by