
Лыжная столица Беларуси
Если, представляя лыжную фабрику, вы думали о запахе свежераспиленного дерева, горах стружек и рабочих со стамесками, то вы застряли в романтике XIX века. Сегодня производство спортинвентаря максимально автоматизировано. Хотя приятный древесный аромат все еще наполняет цеха особым вайбом.
Экскурсию по обновленному лыжному производству для нас проводит заместитель директора Республиканского производственно-торгового унитарного предприятия «Беларусьторг» Станислав Радюкевич. Он предлагает своими глазами увидеть, как делают знаменитые телеханские лыжи. Собеседник вспоминает, что проблемы у белорусского лыжного бренда начались с приходом на рынок пластика. Деревянные модели не выдержали конкуренции с легкими и прочными синтетическими материалами. Однако известный когда-то на весь Советский Союз завод решили не закрывать, а вдохнуть в него новую жизнь. От советского прошлого осталось только название — в честь поселка. Новые лыжи «едут» по новому пути.

Начинка цеха — современное оборудование от ведущих зарубежных и отечественных производителей. На нем можно выпускать почти два десятка видов лыж, под любой вес и рост. Еще одно нововведение — дерево соединили с пластиком. Реализация проекта обошлась в 14 миллионов рублей.
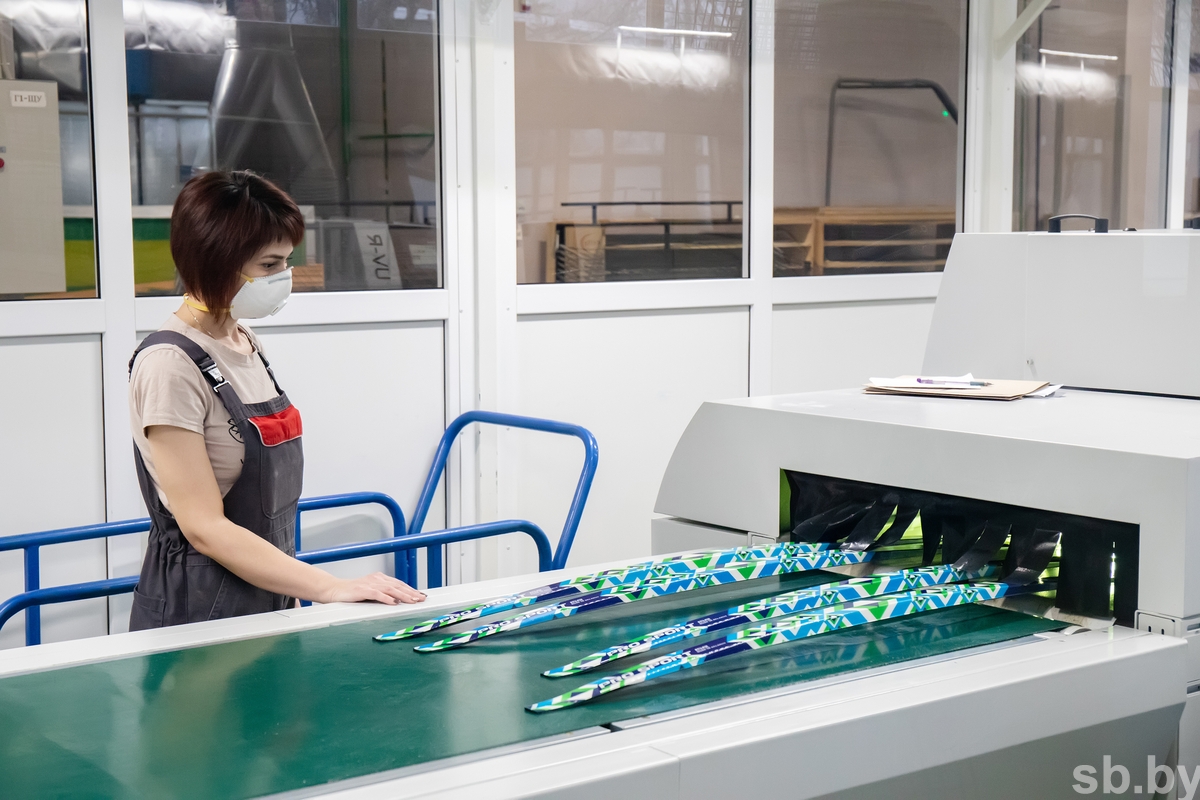
— В сентябре 2018-го Александр Лукашенко поставил перед нами задачу и жесткие сроки — начать выпуск отечественных пластиковых лыж. Недорогих и конкурентоспособных, — вспоминает Станислав Радюкевич. — Производство создавалось и развивалось под кураторством Управления делами Президента. С привлечением научного потенциала БГТУ и Академии наук разработали технологии производства пластиковых лыж и подобрали оборудование. Оно у нас от ведущих мировых производителей в области лыжного инвентаря — Австрии, Германии, Италии, США, Японии в комплексе с прессами белорусского производства, с использованием импортных компонентов. Это позволило наладить выпуск современных пластиковых лыж, не уступающих по своим характеристикам зарубежным аналогам.
Станислав Радюкевич рассказывает, что рынок достаточно узкий, многие друг друга знают:
— Модернизируя производство, мы перенимали опыт у ведущих мировых производителей лыж и в Европе, и в Китае. Были в России на фабриках во Владимире и в Балабаново. На последней производится около одного миллиона лыж в год. Колоссальные объемы! Посмотрели, как производство организовано у них, переняли опыт и создали свое.
Перед запуском серийного производства опытные образцы протестировали на базе отраслевой лаборатории спортивной биомеханики научно-технологического парка БНТУ «Политехник» и выбрали лучшие. Опытную партию из 36 пар лыж протестировали также воспитанники одной из минских спортивных школ.
Запуск нового производства пластиковых лыж для массового потребления состоялся в ноябре 2019-го. В 2021 году предприятие вышло на полную мощность. В стране ежегодно возможно реализовать до 20 тысяч пар, остальной потенциал — на зарубежный рынок. Станислав Радюкевич — об ориентации на массового потребителя, рынках сбыта и проложенной лыжне в Россию:
— Сегодня на склад мы не работаем. Все 6 тысяч пар ежемесячно реализуем. Наши лыжи поставляются во все школы и детские учебные заведения страны. Министерство образования составляет план, и мы уже в июне — июле знаем, какой объем лыж нужно произвести к сезону, можем спланировать свою загрузку. Тесно торгуем с Россией, параллельно ищем новые рынки сбыта. В прошлом году мы продали около 22 тысяч пар лыж. В этом планируем довести этот показатель до 25 тысяч. В денежном выражении это около 1,3 миллиона рублей.
Специалисты следят за мировыми технологиями в области производства спортинвентаря и постоянно совершенствуют их. Прямо на наших глазах две сотрудницы Института химии новых материалов НАН Беларуси тестируют отечественные аналоги импортных материалов.

— Президент поставил задачу, чтобы лыжи были полностью белорусские, — пояснил Станислав Радюкевич. — Деревянную начинку делаем из белорусской осины, гибкий материал для пяточной и носочной части — разработка наших ученых. Покрытие, клеящие и армирующие слои пока импортные, как раз над этим работаем. Специалисты Академии наук сейчас тестируют свою разработку. Политика предприятия — не спешить в ущерб качеству. Поэтому прежде чем внедрить новый материал, тщательно его тестируем, смотрим, как он себя ведет в разных условиях и нагрузках. Думаю, к следующему сезону сможем перейти на производство лыж из полностью белорусских материалов. В перспективе это позволит еще больше снизить себестоимость.
Свои в доску
Мне показали полный цикл производства. Оказалось, бэкстейдж лыжной фабрики еще интереснее, чем субботняя прогулка по лыжне в «Веснянке»! Сам по себе цех вызывает чувство индустриального восторга. Никакой пыли и едкого запаха клея. Вместо этого — чистое и светлое пространство. Цех по производству лыж разбит на несколько участков: изготовление среднего клина, склеивание и обработка, отделка, контроль качества и упаковки. Начинается все с изготовления среднего клина — сердца будущей лыжи. Делают его из осины.
— Заготовки осматривают на дефекты. Если присмотреться, на древесине можно заметить сучки, трещины, — Станислав Радюкевич берет в руки деревянный брус. — Их распознает и удаляет техника.
Полученные бруски перекочевывают на линию сращивания. Здесь на торцах заготовки зарезается множество микрошипов. В следующей части станка они проклеиваются, и заготовки намертво схватываются друг с другом. На выходе получаем ламели до 6 метров в длину. По качеству ламель лучше цельной древесины. Она приобретает необходимую жесткость и менее подвержена короблению и растрескиванию.
…Гудят громадные станки, стрекочут шлифовочные установки, шипят прессовальные машины. Не производство, а песня! Не отвлекая людей от работы, со стороны наблюдаем за следующим этапом производства — многооперационным деревообрабатывающим центром с числовым программным управлением. Ламель загружают в специальный станок, который придает заготовке трапециевидную форму. Пока огромные и дорогостоящие агрегаты ювелирно режут ламель, узнаю, что у лыж своя геометрия. Невооруженному глазу она плохо заметна. Угол наклона боковых поверхностей — два градуса. На глазок такой не сделаешь, да и зачем, когда есть машина!

Далее отправляем нашу деревянную заготовку в литьевую установку, где она обрастает пяточной и носочной частями. Делают их из специальных пластиковых гранул (к слову, тоже разработка наших ученых), созданных специалистами гомельского института механики металлополимерных систем НАН.
— Данный полимер не имеет адгезии с древесиной — говоря простыми словами, его сложно приклеить, — вдается в технические детали Станислав Радюкевич. — Наши ученые разработали такой состав, который дает хорошую адгезию с древесиной, замок получается очень прочным. Попробуйте — не отломаете!
На следующем этапе мой словарный запас пополнился словом «препрег». Это пропитанные эпоксидными смолами стеклоровинги, которые придают лыже жесткость. Пластиково-деревянную заготовку аккуратно заворачивают в листы препрега и укладывают в металлическую кассету. Этот «сэндвич» отправляется под пресс и остается там при температуре 120 градусов на 20 минут. В таких условиях препрег лучше проявляет свои армирующие и склеивающие свойства. Затем — этап охлаждения. Температура опускается до 14 градусов. Кстати, пресс изготовили в филиале «Кузлитмаш» компании БЕЛАЗ. Над нагревательными элементами и кассетами станка работали в ОАО «НПО Центр» НАН Беларуси. Куда ни глянь — отечественные разработки!
Анатомия лыж
Наша лыжа практически готова. Нарезается желоб — для курсовой устойчивости. И лыжа отправляется на шлифовальный станок, который задает нужные параметры ее нижнему скользящему слою. На этом этапе наносится штайншлифт. Для тех, кто не учил немецкий в школе: это переводится как «нанесение структуры».— Нечто подобное вы могли видеть в автомобильных покрышках. Летняя и зимняя резина отличается друг от друга рисунком и глубиной протектора. С лыжами то же самое, — проводит параллели Станислав Радюкевич. — Штайншлифт помогает улучшить скольжение лыж в определенном погодном диапазоне. Мы выбираем универсальный, который может работать при температуре от минус одного до минус восьми градусов. Но вообще мы можем делать разную шлифовку — и для мягкого, и для жесткого снега. При необходимости наносим степ-насечку. При ходьбе классическим ходом она не позволяет лыже проскальзывать назад.

Наши лыжи уже на финишной прямой, точнее, на участке отделки. Осталось покрыть их лаком для повышения износостойкости. Дело в том, что в искусственный снег добавляются присадки, которые не лучшим образом воздействуют на все составляющие лыжи. После сушки их можно забирать на упаковку. Наконец, осталось самое интересное — выбрать пару для каждого изделия. Да-да, изначально пары они не имеют. Идеальные «вторые половинки» подбираются в конце.
Мне конструкция белорусских лыж чем-то напомнила сэндвич. Внутри — деревянный сердечник из облегченной древесины. Он заворачивается в армирующий слой, который обеспечивает необходимую жесткость. Сверху — модифицированный АБС-пластик, в качестве скользящей поверхности — полиэтилен высокой плотности. На выходе получаем лыжу весом около 700 граммов. Новинка предприятия — облегченная модель. Благодаря среднему клину с воздушными каналами она стала легче своей предшественницы на 150 граммов!
Когда на фабрике говорят о научном подходе, не преувеличивают. Здесь организован многостадийный контроль качества. Специальная лаборатория испытывает материалы перед запуском партии в производство. Для контроля качества произведенной продукции наряду с производственной лабораторией филиала создана лаборатория на базе БГТУ, где лыжи испытывают по всем физико-механическим параметрам — массе, положению центра тяжести, стреле прогиба, разрушающей нагрузке…
Профессиональные кадры, жесткий контроль качества на всех участках производства и отделки, высокое качество материалов позволяют выпускать высокотехнологичные современные спортивно-беговые лыжи. Средняя стоимость белорусской пары — около 60 рублей. Это гораздо дешевле зарубежных.
Лыжи — товар сезонный. Его производство начинается летом, потому что к старту сезона спортинвентарь должен ждать на полках своего покупателя. Но остальную часть года оборудование не простаивает. Оно переориентируется на производство мебельных щитов — тоже экспортно ориентированный продукт. Кстати, оборудование многофункциональное, при необходимости при сравнительно невысоких капиталовложениях его можно приспособить для выпуска и другого схожего спортивного инвентаря. В будущем на предприятии планируется наладить массовый выпуск облегченных лыж.
gorbatenko@sb.by