Metal cutting craftsmanship
Strong seams and short circuit welding — let us unveil the ‘recipe’ for making a perfect electric bus

Sparkling metal sheets, steel pipes, aluminium profiles and other blanks in the production workshops of BKM HOLDING, formerly known as Belkommunmash [leading Belarusian manufacturer of modern urban electric transport], turn into stylish public transport in less than a month. The lion’s share of credit goes to the welders for their tireless and high-quality work. Specialists who know how to treat metal properly, harnessing its hardness and strength, have always been worth their weight in gold. From this perspective, BKM HOLDING is a treasure trove. Let us get an insight into the work of craftsmen who create electric vehicles.

Multi-purpose specialists
A layman observer may associate the work ongoing in the Belkommunmash body shop with an incomprehensible cacophony of sounds, knocks and sheaves of sparks from all sides. Wherever you look, there are tough men dressed in sturdy canvas overalls and gloves bent over metal parts with burners in their hands.Igor Velinsky has a rare profession — a 4th category resistance welding machine operator. He has celebrated his anniversary recently — 30 years of work at the Belkommunmash plant — and received the Medal for Labour Merits. There are 11 people in his team, most of whom are welders. They are all multi-purpose and interchangeable specialists.
While making a casing for the battery, which will be installed on the roof of the electric bus, Igor provided some details of his work. “It is necessary to weld together blanks of various sizes, from large metal sheets to parts of a couple of centimetres,” he noted. “For this purpose, different types of welding are used: spot or contact welding, when metal sheets are welded by a short circuit and the seams look like rivets, as well as argon arc and semi-automatic welding.”
Any welder in the company can read drawings no worse than an engineer. After all, all the parts need to be correctly positioned and assembled into a single whole. Counting on luck does not work — vehicles designed for different countries and cities significantly differ from each other. It is often necessary to deal with new modifications.
On the one hand, it is captivating, but on the other hand, this may decrease the pace of work. Delays are in no one’s interest since the company is literally inundated with orders, and the remuneration is based on the piece plus-bonus system.
Let us be honest — welders’ work is no piece of cake. They constantly work with high temperatures, red-hot metal and complex equipment. Therefore, welders are entitled to early retirement, to receive milk or juice on a daily basis for harmful working conditions, and up to 41 days of vacation. Do young people strive to work in such conditions? Igor Velinsky expressed an optimistic point of view confirming that there were smart guys.
They say that specialists who have tried their luck not only at different enterprises, but also in other countries eventually seek employment at BKM HOLDING. Thus, a young man who previously worked in France is now getting a job with this Belarusian enterprise. According to migrant workers, “Offers from abroad are enticing, and the salary seems alluring for Belarusians. However, a lot of drawbacks come to light later. The cost of food products and rental housing eats up the lion’s share of earnings resulting in the net profit that turns out to be the same as one can earn in Belarus — in the native country, among your nearest and dearest, communicating in a familiar language.”

Steel beauty
The largest parts of electric-powered public transport related to the body frame are the base, roof and sidewalls. A team of five people, headed by Valentin Leshok, is engaged in their manufacture. Valentin Leshok boasts colossal work experience — as many as 46 years.When entering the tram, the carriage seems to be small and compact. During the manufacturing process, however, the body roof looks huge, as if lost in the distance. “The roof length of this carriage is 1,259 centimetres, plus two more cabins,” the master explained. “Each roof model has different sizes and parts. We do everything exactly according to the drawings. We use argon arc welding using a mixture of gas and carbon dioxide. The seam with such welding turns out to be durable and neat at the same time. Actually, we still apply a grinding machine later. After all, the surface were the cladding is attached must be perfectly smooth.”
Valentin admitted that despite many years in the profession, he never got enough of the fascinating beauty of red-hot steel being melted. The sight is truly mesmerising!
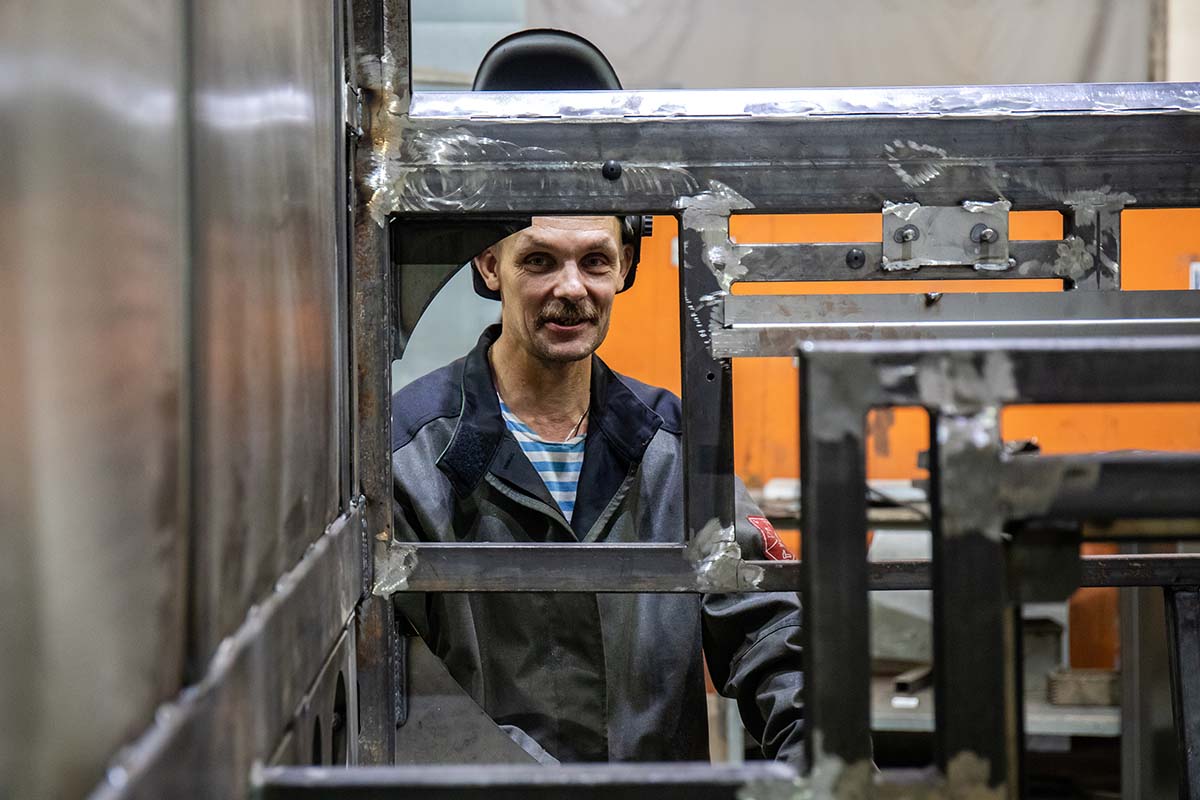
Sergei Tishkevich
Assembly workshop at BKM HOLDING
![]()


Experience for the youth
The frame for the future tram is made up of disparate components through the efforts of the team, where Sergei Tishkevich works. The welders assemble the future body. It is necessary to do the work quickly and efficiently, that is why they use semi-automatic welding. “This work is not hard, it is fine,” Sergei broke stereotypes on the spot. “I have got used to welding sparks due to many years of work. I have been working at this company since 2000. I like it here, and I am pleased with the salary. I have recently taught welding to college students who came to practice. I must say right away — there were all sorts of people. There were students who showed keen interest and tried their best, and there were those who just wanted to serve their practice period and leave.” Sergei admitted that they produced at least 25 vehicle bodies in a month. QUOTE
Irina Vezitskaya, Deputy General Director of BKM HOLDING for Ideological, Social Work and Personnel Management,“The company employs 69 welders. Most of them, 52 people, are employed in the body shop. The team is coherent and well-established. Nevertheless, vacancies for welders are still available since production volumes are constantly growing. By the way, the company has issued an order on financial incentives for employees who attract qualified personnel of working professions. This approach has helped us to employ five specialists. The company also envisages additional payments for the internship supervision, as well as various social benefits. The average salary last month was almost Br2,900.”
By Oksana Nevmerzhitskaya
Photos by Aleksandr Gorbash