Модернизация нон-стоп
На БГПЗ перерабатывается весь добываемый в стране попутный нефтяной газ. До конца 2024 года эта цифра должна составить 203 млн кубометров. Из этого объема произведут 112 тысяч тонн широкой фракции легких углеводородов, а из нее, в свою очередь, — 86 тысяч тонн сжиженного газа, 26 тысяч тонн бензина газового стабильного и 49 млн кубометров отбензиненного газа.Директор БГПЗ Сергей Пашков подчеркивает:
— Сырья собственной добычи достаточно для обеспечения производства автомобильного сжиженного газа марки ПБА под полную потребность внутреннего рынка.
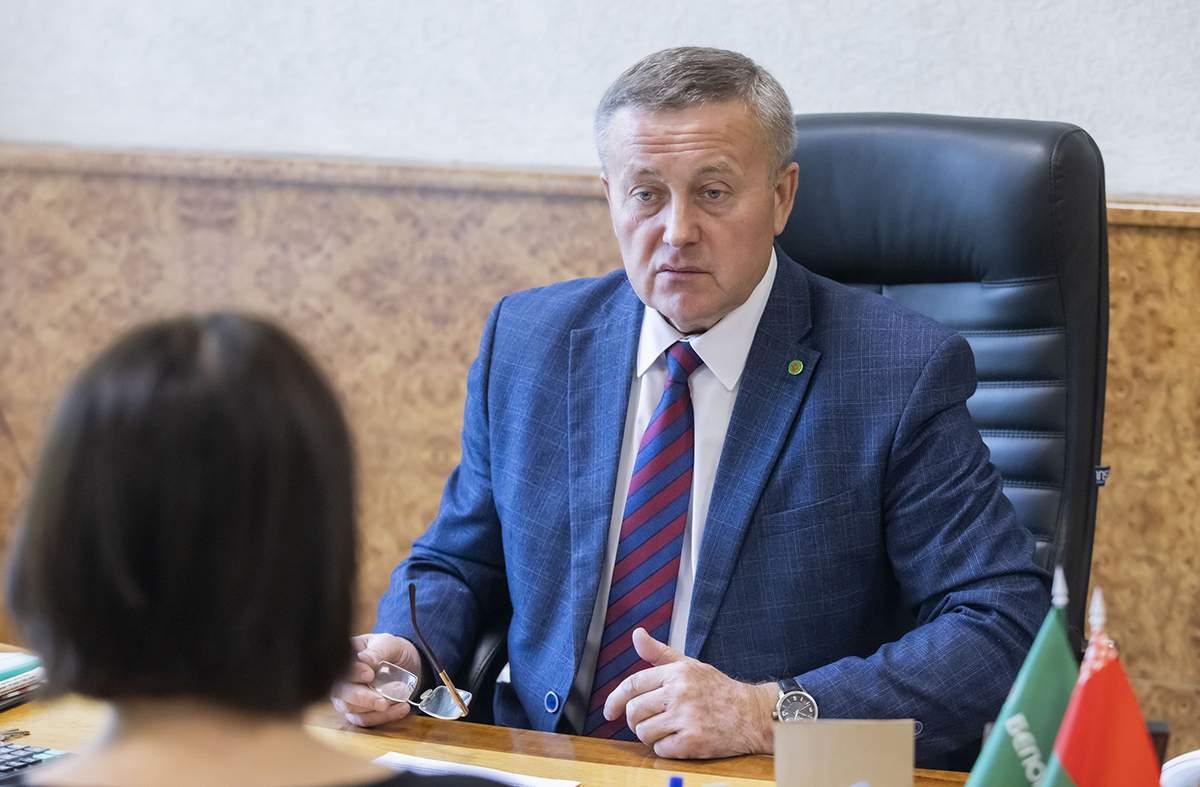
Модернизация на заводе проходит в режиме нон-стоп. К примеру, сейчас реализуется проект по реконструкции концевого блока охлаждения на участке компримирования газа для сокращения экономических потерь при работе объектов и повышения надежности их эксплуатации. Например, снизится коррозионное влияние транспортируемого газа на технологические трубопроводы.
Заместитель директора БГПЗ по строительству, общим вопросам и идеологической работе Сергей Горленко объясняет:
— Реконструкция позволит укоротить протяженность коммуникаций системы компримированного нефтяного газа с 180—200 метров до 30—40. Кроме того, уменьшится поверхность теплообмена, что позволит сконденсировать и сепарировать компоненты, выпадающие в трубопроводе.
Ремонтные работы и, как следствие, экономические затраты при эксплуатации объектов завода сведутся к минимуму.
Не газом единым
— Завод перерабатывает не только газ — мы еще и энергетики, — обращает внимание на специфику работы Сергей Пашков. — На БГПЗ две фотоэлектрические станции: на головных сооружениях — мощностью 55,2 МВт, на территории завода — мощностью 3,75 МВт.Объем выработки электрической энергии составляет более 400 млн кВт·ч в год, в том числе 63 млн кВт·ч — от фотоэлектрических станций. Из всего объема 250 млн кВт·ч отпускается обособленным подразделениям предприятия, 75 млн кВт·ч потребляет завод, а остальная электроэнергия реализуется ГПО «Белэнерго».
Острый вопрос для реального сектора экономики — замещение импортного сырья, оборудования и расходных материалов отечественными аналогами.
Первый заместитель директора — главный инженер БГПЗ Денис Стальмах рассказывает:
— Работа по импортозамещению у нас идет давно, непрерывно и дает хорошие результаты. Мы активно работаем с Институтом механики металлополимерных систем имени В. А. Белого НАН Беларуси. С 2016 года оттуда поставляют клапанные пластины для поршневых компрессоров. Это приносит заметную экономию затрат, потому что такие же от зарубежных производителей стоят значительно дороже.С 2022-го у белорусской фабрики покупаем фильтры предварительной и тонкой очистки воздуха для когенерационной технологической установки (блок станции № 2, который предназначен для выработки электроэнергии).
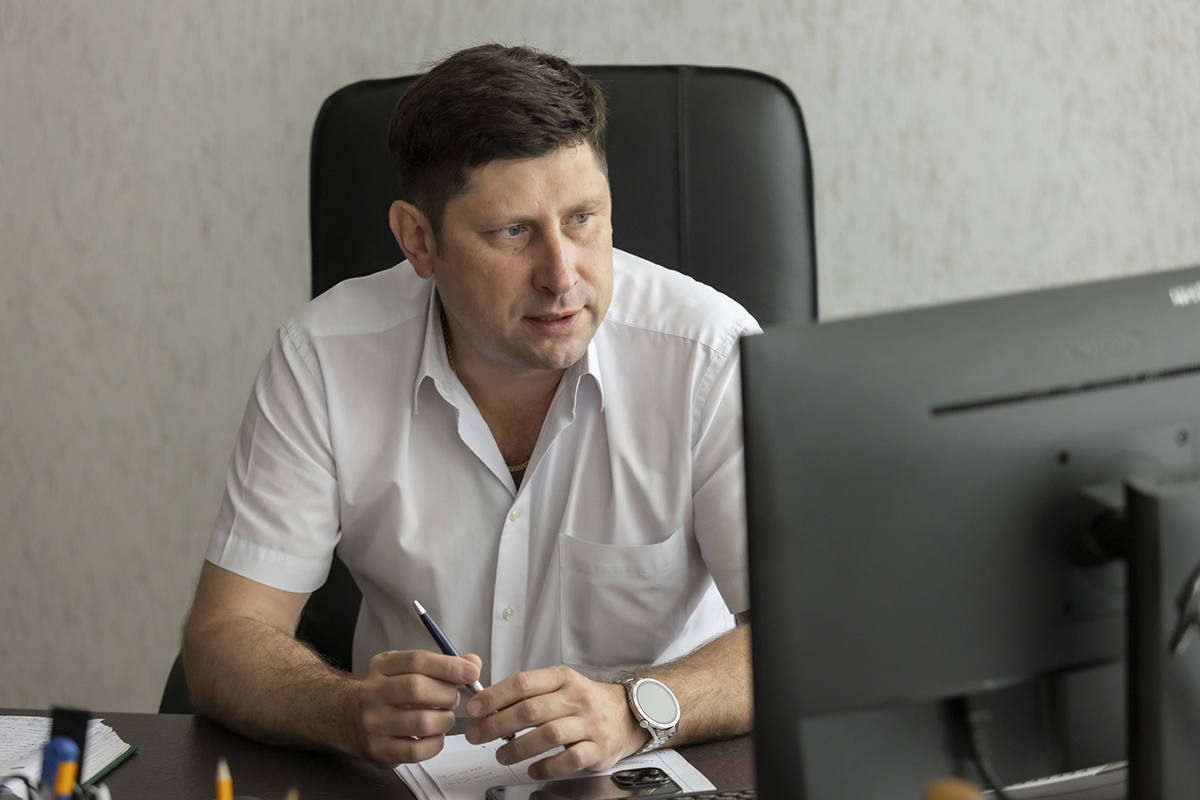
Опытно-промышленную эксплуатацию проходит масляный фильтр — он устанавливается на газопоршневых агрегатах (блок станции № 1). Не прекращается работа по снижению себестоимости продукции — только в 2023-м в этом направлении реализовано 28 мероприятий. Экономия превысила 5 млн рублей.
Главные сокровища — знания и опыт
Мы рядом с установкой газофракционирования, она относится к участку переработки газа. Ее задача — разделение на индивидуальную фракцию ШФЛУ (широкая фракция легких углеводородов) собственного производства и привозную, которая поступает с Мозырского нефтеперерабатывающего завода и из ОАО «Нафтан». Эти два вида сырья смешиваются и последовательно разделяются по температурам кипения в ректификационных колоннах.Начальник производства — главный технолог БГПЗ Андрей Павловец на заводе работает уже 17 лет.
— Меняются технологии, все становится более современным, — говорит он. — Наши главные сокровища — знания и опыт, а они должны быть такими же прочными и солидными, как вот эта установка.
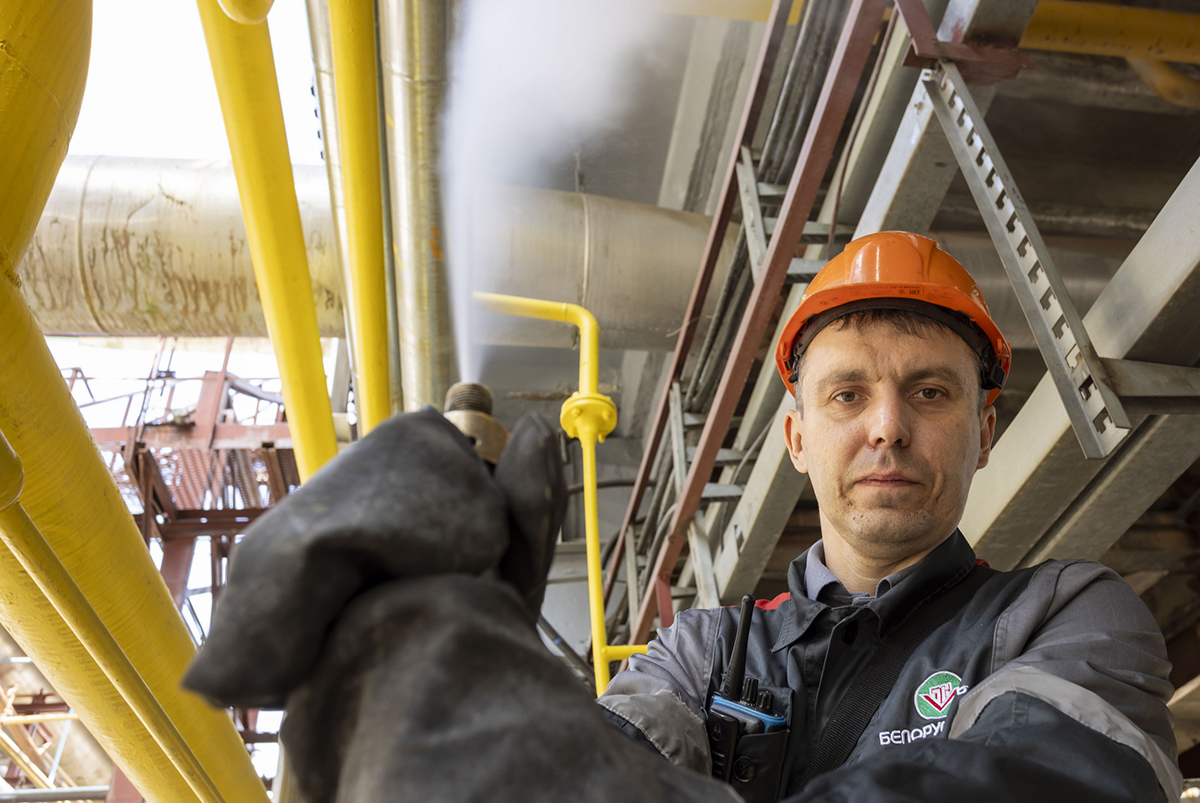
Линия автоматизирована, во время съемок мы встретили только двоих операторов, которые занимались отбором ходовых проб.
— В зависимости от того, какое оборудование у нас работает, мы отбираем ПБА, пропан, сумму бутанов, ШФЛУ собственной выработки, — объясняет Андрей Павловец. — Когда включаются и другие колонны, то, соответственно, добавляются пробы. Вообще, текущих анализов десятки, и цели у них разные. В основном определяем фракционный состав — это база, от нее зависят другие показатели.
Цифровой завод
Ходовые анализы проводятся для того, чтобы любые минимальные отклонения от заданных значений можно было выявить на промежуточном этапе, откорректировать режим работы установки и в итоге получить продукт идеального качества. Все пробы исследуются в химической лаборатории БГПЗ. Отправляемся в ее самое сердце — хроматографическую комнату.Каждый из 13 хроматографов выполняет свою задачу. В сутки сюда поступает около 100 проб — все они проходят тщательный анализ на определение компонентного состава. Во время нашего посещения проводились пробы готового к реализации сжиженного углеводородного газа. По итогам он должен соответствовать газу по стандарту СТБ 2262—2012 марки ПБА.
Заведующая лабораторией Людмила Могильная объясняет:
— Оборудование новое, также недавно к нему добавились аппараты «Хроматэк-Кристалл», «Кристаллюкс». Все хроматографы автоматизированы, результаты рассчитывает программа — это позволяет оперативно проводить испытания и в режиме онлайн передавать специалистам завода. Причем такие исследования мы проводим не только для себя, но и для сторонних организаций.
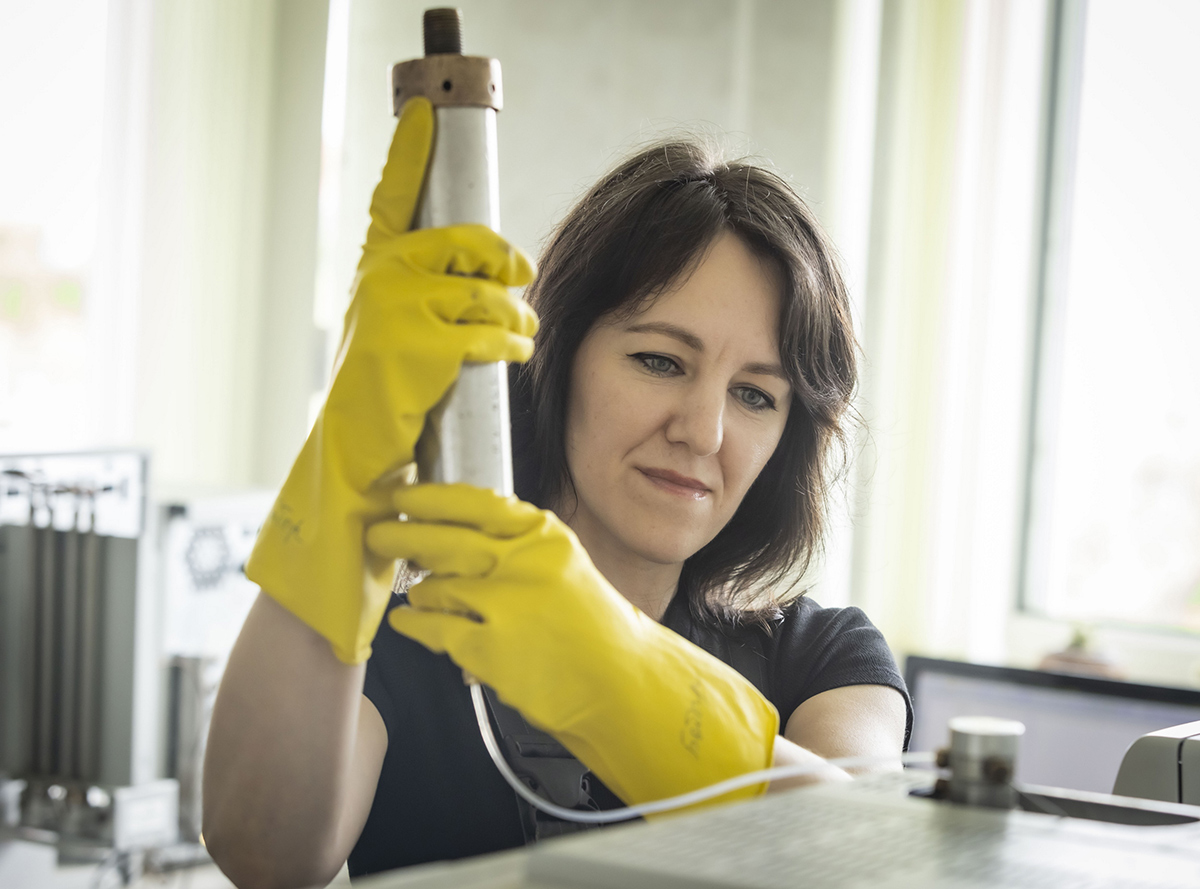
БГПЗ продолжает успешно решать задачи, поставленные на этот год, в том числе своевременно и эффективно перерабатывать попутный нефтяной газ и привозное сырье, обеспечивать максимально возможную выработку электрической энергии, бесперебойную работу оборудования и завода в целом, минимизировать производственные затраты. Также важное и перспективное направление развития — цифровизация производства.
Директор предприятия Сергей Пашков конкретизирует:
— Создание информационно-аналитической интегрированной системы цифровизации БГПЗ «Цифровой завод» позволит консолидировать все внутренние и внешние процессы производства в единое цифровое пространство, помогая оперативно получать информацию и отслеживать работу предприятия в режиме реального времени, повышать скорость принятия управленческих решений, сокращать потребление топливно-энергетических ресурсов, ускорять реакцию на отклонения в работе оборудования.
В апреле на БГПЗ успешно произвели плановый остановочный ремонт, во время которого выполнили все необходимые профилактические работы, связанные с обследованием, ревизией и диагностикой эксплуатируемого оборудования. Все это позволит предприятию функционировать без ремонта до 2026-го.
— Таким образом, завод опробует переход на двухгодичную структуру ремонтного цикла. Это потребовало серьезной подготовки в организации работ и материального обеспечения, ведь в период остановочного ремонта мы выполнили все, что было намечено на два года вперед. Переход позволит нарастить объемы товарной продукции и оптимизировать затраты предприятия, — поделился результатами и планами руководитель.
5 млн рублей сэкономлено в 2023 году благодаря реализации 28 мероприятий, направленных на снижение себестоимости продукцииseveryanova@sb.by
Фото предоставлены компанией «Белоруснефть»