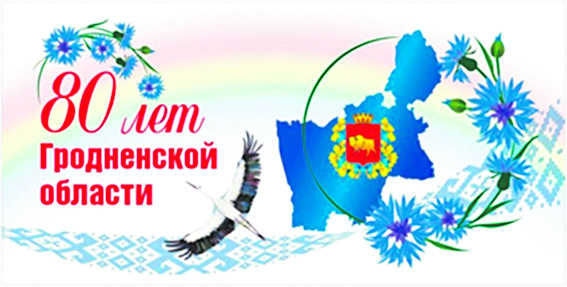
Более века в небольшом городском поселке Красносельский производят стратегический продукт и основу строительной отрасли — цемент. В этом году предприятие отметило 110‑летний юбилей. Сегодня здесь сделана ставка на модернизацию и оптимизацию затрат. Благодаря этому удается снижать себестоимость продукции, удовлетворять спрос потребителей, постепенно наращивая объемы, и улучшать благосостояние работников.
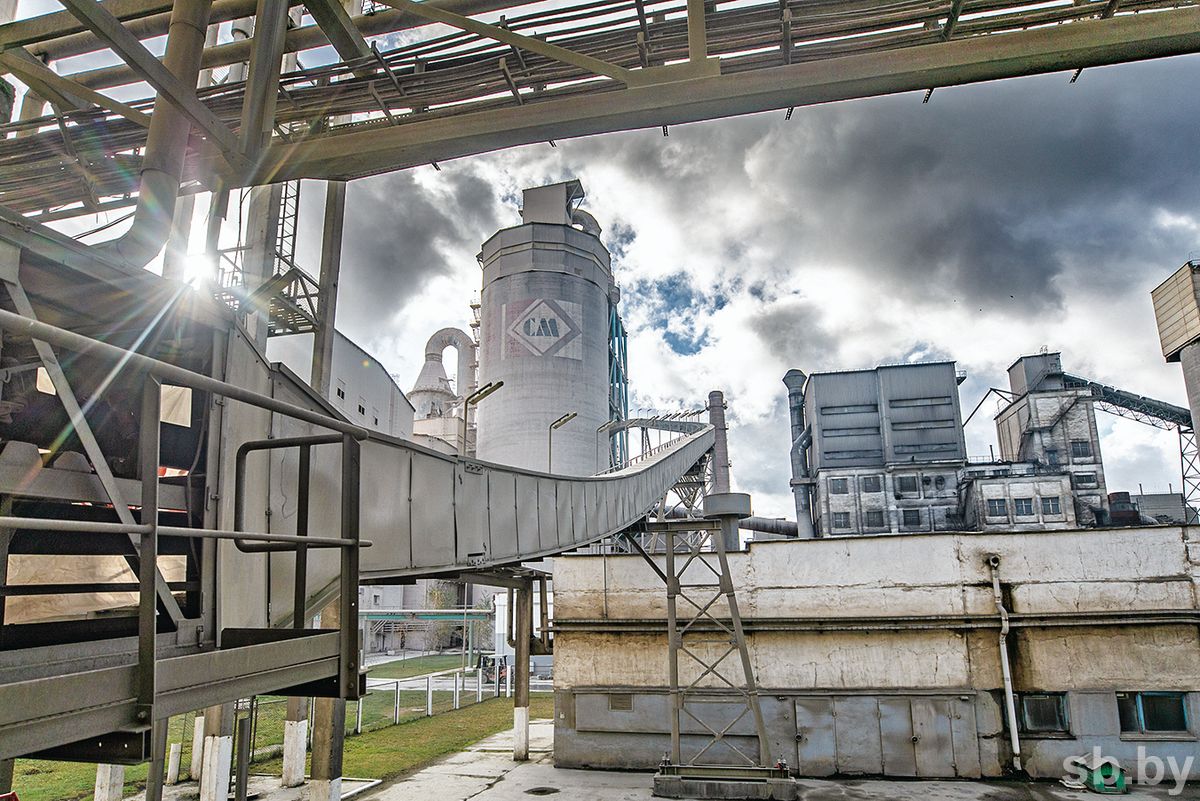
Тернистый путь
Новый виток развития предприятие получило в 2019 году, когда Президент подписал Указ № 181 «Об организациях цементной отрасли», в соответствии с которым акционерному обществу была оказана государственная поддержка. В частности, отсрочки по погашению долгов за топливно-энергетические ресурсы, по полученным кредитам. В результате спустя год удалось стабилизировать положение и увеличь объемы производства. Уже в 2021 году был установлен рекорд по поставкам цемента на экспорт. Немаловажную роль сыграл и тот факт, что все белорусские производители цемента вошли в холдинг «Белорусская цементная компания». С тех пор внутренняя конкуренция ушла, появилась единая сбытовая политика, общие закупки, что позволило снизить цену на импортные сырьевые компоненты.— После того как в 2022‑м Евросоюз ввел санкции, из трех заводов мы оказались в самой худшей ситуации, — рассказывает заместитель генерального директора по экономике Александр Голда. — До этого наш экспорт был нацелен на Запад: треть уходила в Польшу, Украину и Прибалтику. Более 60 процентов газосиликатных блоков продавалось в Евросоюз. Таким образом, было принято решение об оптимизации структуры продаж. Теперь мы закрываем весь внутренний рынок, в то время как наши коллеги из Могилевской области ведут торговлю с Россией. Это что касается цемента, блоки мы также начали поставлять в Россию. По результатам девяти месяцев этого года мы неплохо сработали. Так, имеется рост объемов производства продукции в фактических ценах — 120,8 процента, в натуральном выражении мы продали цемента на 113,6 процента, блоков — 120 процентов. Экспорт к уровню 2023 года вырос на 137,2 процента.
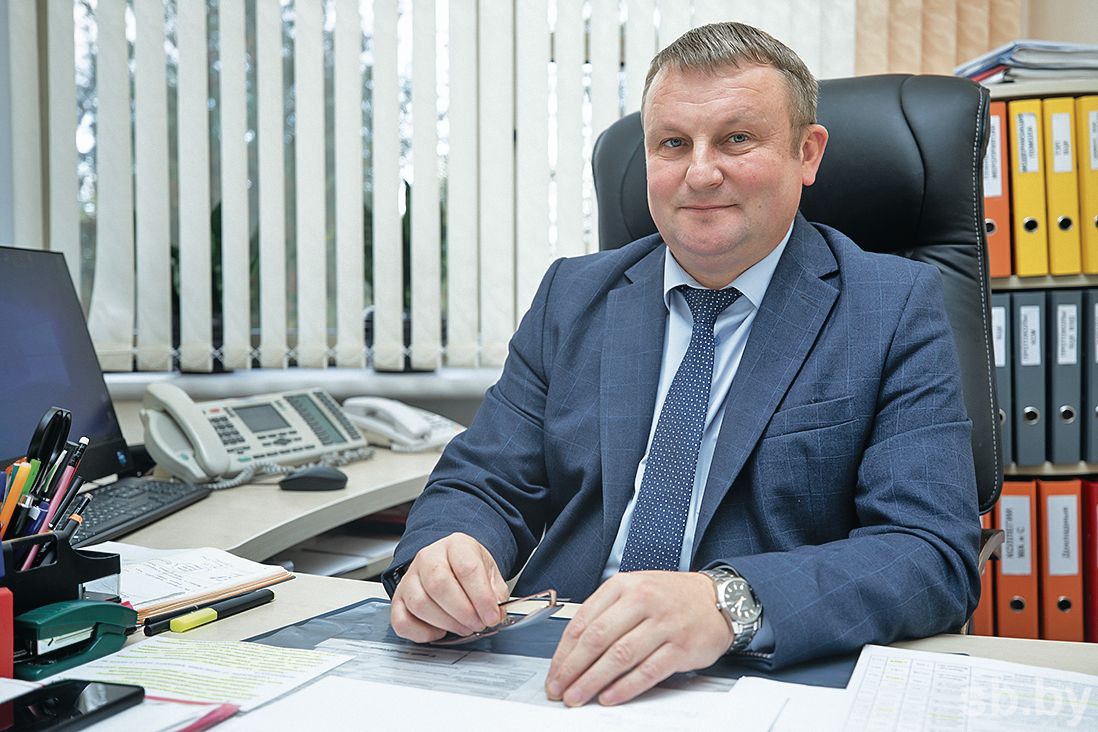
Достичь данных показателей, уверен Александр Владимирович, не удалось бы без реализации инвестиционных проектов. Подробнее с ними познакомились на производстве. Держим путь в сердце предприятия — цементный завод.
Слагаемые успеха
Заместитель директора по производству филиала № 1 «Цементный завод» Евгений Волощик поведал, какие этапы включает производственный процесс:— Цемент состоит из клинкера и различного рода добавок. Изначально изготавливается портландцементный клинкер. Получив мел, глину, железо и алюминийсодержащие добавки с карьерной влажностью около 25 процентов, мы должны их высушить и измельчить. Затем сырьевая мука обжигается в печи при температуре до 1500 градусов. Таким образом начинается частичное плавление компонентов, что приводит к образованию гранул клинкера, который перемалывается, и получается цемент. В сутки наша печь производит пять тысяч тонн клинкера, из которого выходит 5,5 тысячи тонн готового продукта.
Всем процессом круглосуточно управляют машинисты мельниц и обжигальщики, а контролируют инженеры-технологи в центральном пункте управления (ЦПУ). По словам Евгения, это помещение — мозг производства.
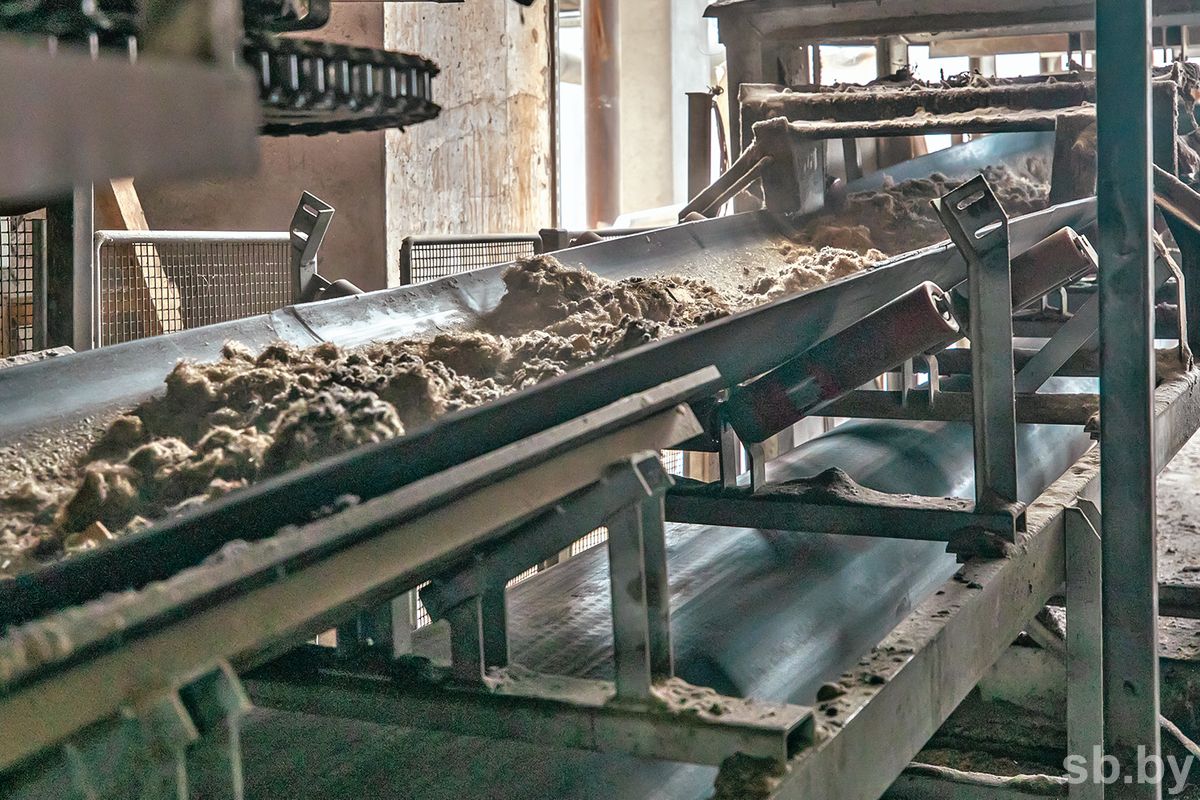
— Работники ЦПУ следят за качеством материалов на каждом этапе, количеством подаваемого сырья, расходом топлива, температурами и массой других показателей. От их действий зависит результат на выходе. Для проведения оперативных действий машинисты держат связь с рабочими по рации либо мобильной связи. У каждого есть рабочий телефон.
Поскольку энергетическая составляющая при производстве клинкера довольно высокая, здесь постоянно работают над снижением энергоемкости и совершенствуют структуру его топливного баланса. До 2012 года предприятие работало на природном газе, который является самым дорогим топливным ресурсом. Когда ввели в эксплуатацию новую линию по производству клинкера сухим способом, удалось перейти на уголь и частично снизить затраты. Однако проблема заключалась в том, что и уголь также импортное топливо.
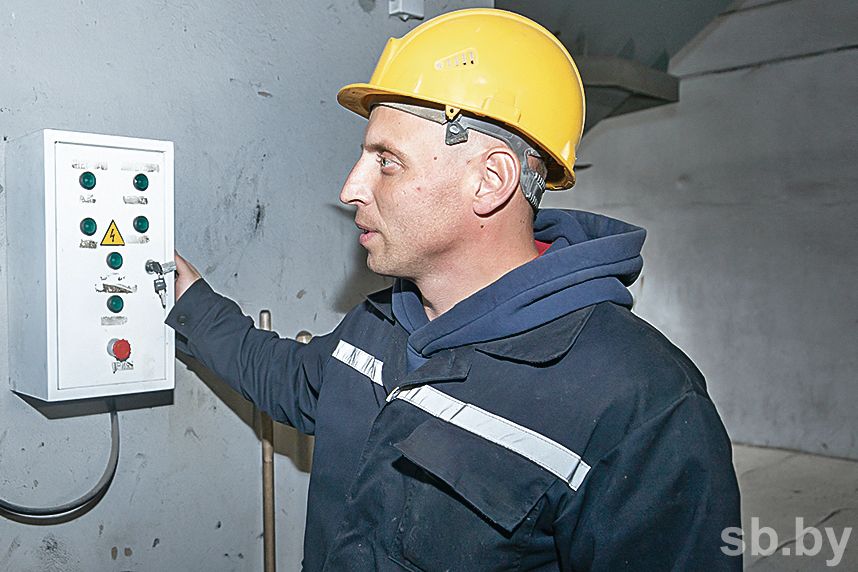
— В связи с этим было реализовано несколько проектов по замещению угля, — рассказывает Евгений. — Сегодня основной вид замещающего топлива — торф, который поставляют отечественные торфобрикетные заводы, в частности Лидский, Ляховичский, Березовский. В 2022 году запустили торфогенератор, который предназначен для подготовки сырьевой муки. С его помощью в час мы производим до 400 тонн муки.
Еще один проект, который ранее в Беларуси нигде не был реализован, связан с использованием RDF-топлива в процессе обжига клинкера. Эта линия была введена в строй в 2021 году.— Сегодня благодаря ей мы сжигаем альтернативные виды топлива. Такие как волокно синтетическое из шинного корда, костра льняная, измельченная ветошь, древесные пеллеты. Также начали использовать белорусский нефтяной кокс, — отмечает Евгений. — Недавно получили 9,7 тонны RDF-топлива с Гродненского завода по утилизации и механической сортировке отходов. Оно получается из твердых коммунально-бытовых отходов. В перспективе наладить промышленные поставки такого топлива на предприятие, что в значительной мере заместит пылеугольное для производства цемента.
В целом сегодня на предприятии до 30 процентов топлива замещают торфом и альтернативными видами. Это довольно высокий показатель, позволяющий значительно экономить и снижать себестоимость конечного продукта. К слову, цель производства — и в дальнейшем увеличить показатели замещения.
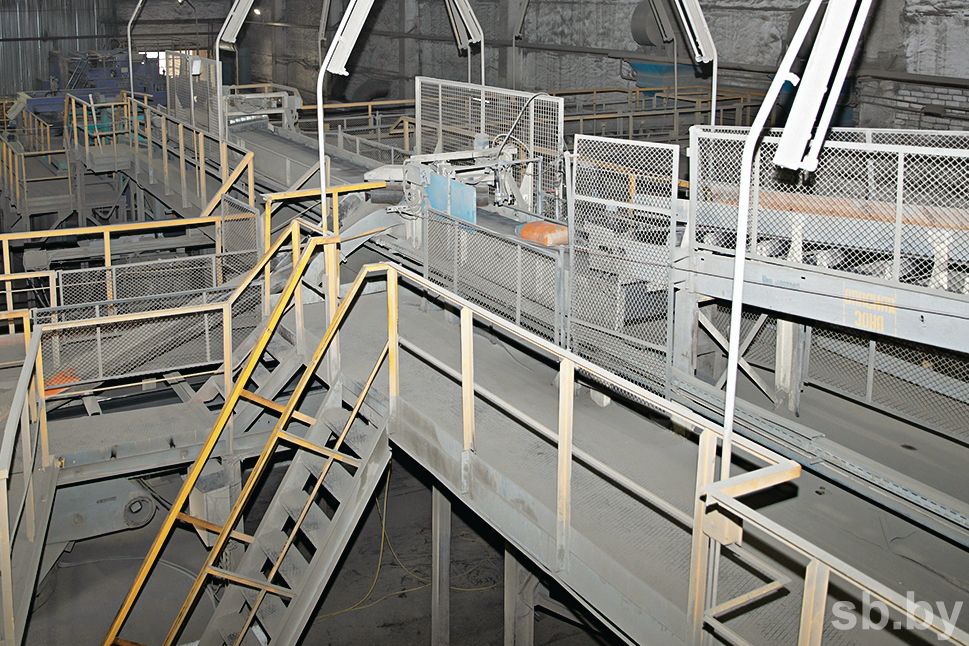
— Благодаря своевременной модернизации и оптимизации затрат по итогам девяти месяцев этого года имеем рентабельность продаж около 8,7 процента. Погашены долги за топливно-энергетические ресурсы, в этом году погасим инвестиционные кредиты. Удалось повысить на 121,6 процента по сравнению с аналогичным периодом прошлого года зарплату работникам. Она составляет в среднем 2200 рублей, — отмечает Александр Голда.
Высокая планка
Помимо сокращения затрат на топливно-энергетические ресурсы постоянно ведется работа над повышением качества продукта. Так, благодаря модернизации одной из мельниц появилась возможность многократного помола сырья для получения оптимального гранулометрического состава цемента — это более высокий класс продукта, который сегодня востребован и на внутреннем, и на внешнем рынках.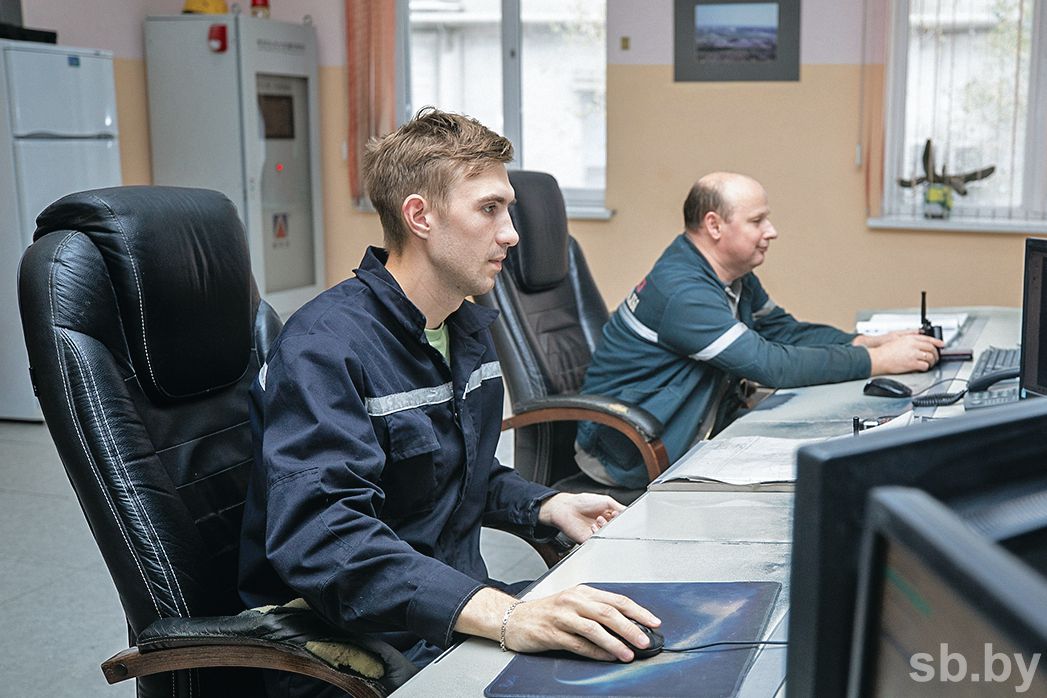
— В данный момент загрузка мощностей у нас более 100 процентов. Товар не залеживается на складе. Сегодня потребитель требует больше, чем три завода вместе могут произвести, — констатирует Евгений Волощик.
Александр Голда добавляет, что красносельский цемент многие годы успешно конкурировал с мировыми производителями на европейских рынках именно за счет качества.
— Чтобы увеличить объем производства продукта высокого класса, планируем строительство еще двух цементных мельниц, которые будут работать по замкнутому циклу с производительностью по 150 тонн в час. Сейчас у нас каждая мельница производит по 45 — 50 тонн цемента. А также возведение новых силосов для цемента, двух линий упаковки его в мешки и современного клинкерного склада. Новое оборудование позволит еще больше снизить себестоимость продукции, благодаря чему мы в дальнейшем сможем конкурировать на рынке.
ЗДОРОВЬЕ ЛЮДЕЙ
ОАО «Красносельскстройматериалы» имеет свой санаторий «Пралеска», расположенный в живописном лесу на берегу озера Лазурного. Каждый работник предприятия, а также пенсионеры и ветераны труда могут купить путевку в свой санаторий со значительной скидкой — им необходимо оплатить 20 процентов, пенсионерам и ветеранам холдинга «Белорусская цементная компания» — 10 процентов.
— В санатории созданы условия для оказания полного объема диагностических и лечебно‑реабилитационных услуг по следующим профилям: болезни системы кровообращения, болезни органов дыхания, болезни костно‑мышечной и соединительной ткани, болезни нервной системы, — рассказывает главный врач Николай Автух. — Гости размещаются в двух жилых корпусах с общим количеством 120 мест. Приезжают отдыхать к нам и гости из‑за рубежа.
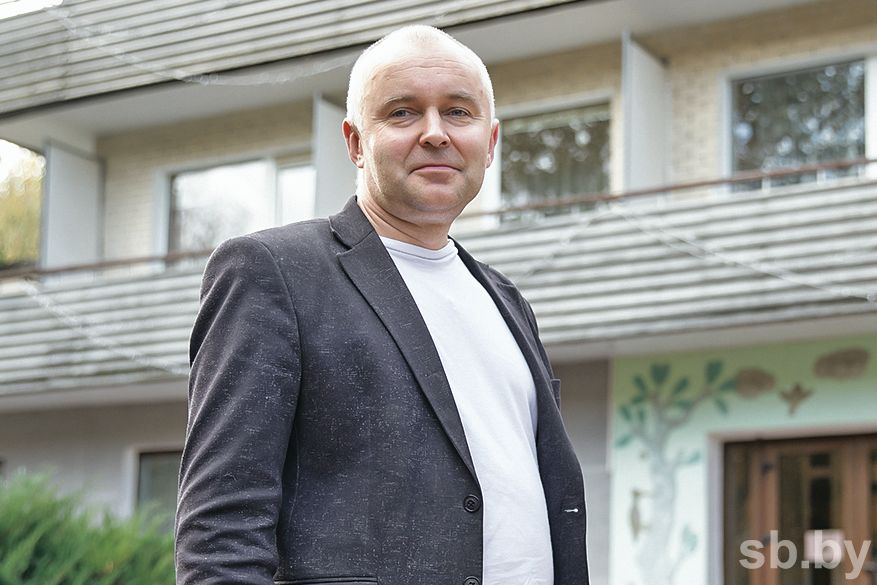
Руководство предприятия выделяет средства на приобретение самого современного медицинского оборудования. Здесь используется магнито‑ и лазеролечение, электросветолечение, грязелечение, водолечение, комплексное СПА‑лечение, лечебная физкультура, гидрокинезотерапия и многое другое.
ЦИФРА
В ОАО «Красносельскстройматериалы» трудятся более 2200 человек. Технологические линии предприятия сконцентрированы в четырех производственных филиалах в городском поселке Красносельский, Гродно и Сморгони.
УНП 590118065